The importance of industrial endoscope in aircraft troubleshooting
The importance of industrial endoscope in aircraft troubleshooting
Any failure or potential failure of the aircraft is a serious threat to flight safety, so it must be treated with caution. Even if it is only suspected that an unknown object (such as a small piece of debris) enters the aircraft engine, a comprehensive inspection should be carried out, especially inside the engine. According to the requirements of aircraft maintenance manual and airworthiness instructions, industrial endoscope is often required, which is a very intuitive detection method to clarify the status of aircraft.
With the development of manufacturing technology, endoscopic inspection technology has been widely used in many fields, such as pressure vessels, industrial pipelines, reactors, heat exchangers and other welding internal surface quality, which are the inspection objects of industrial endoscopes. In the aerospace field, it is used to check whether turbine engine blades are damaged, which is faster, more accurate, and efficient than traditional hand touch and visual inspection.
It is naturally unwise to disassemble the engine without identifying the fault. The interior of the engine can be observed without disassembly using an industrial endoscope. The process is also a challenge for inspectors. It is necessary to find the damaged area through some recognizable traces (such as bolts and nuts) under the guidance of the detection image. A good industrial endoscope can play a better auxiliary role.
For example, JEET JX series motor-driven 3D measurement videoscope has image processing capabilities such as automatic light output adjustment lighting system, adaptive noise reduction, and dark enhancement, so that it can perform stably under variable detection conditions. Whether in dark or reflective or looking for small defects in a wide range of living areas, inspectors can find traces of defects or faults in clear images. The equipment also has the 3D measurement function of the dry phase scanning technology, which can accurately measure a series of defect characteristics.
After the endoscope inspection of aircraft components, a detailed inspection report will usually be issued, including the description of the detected defects or faults, as well as high-quality inspection images and video data. The inspectors will make the final decision based on this information, often with three results: the aircraft could continue to fly after being released, would be authorized to fly back to the base for maintenance, would be replaced the engine.
The maintenance cost of aircraft engines may exceed one million dollars, and the cost of replacing engines is more expensive. Therefore, inspectors need to produce accurate and visual fault evidence, which will affect whether they can make wise decisions. Industrial endoscopes can achieve this goal, which also highlights the important role of industrial endoscope in aircraft fault diagnosis.
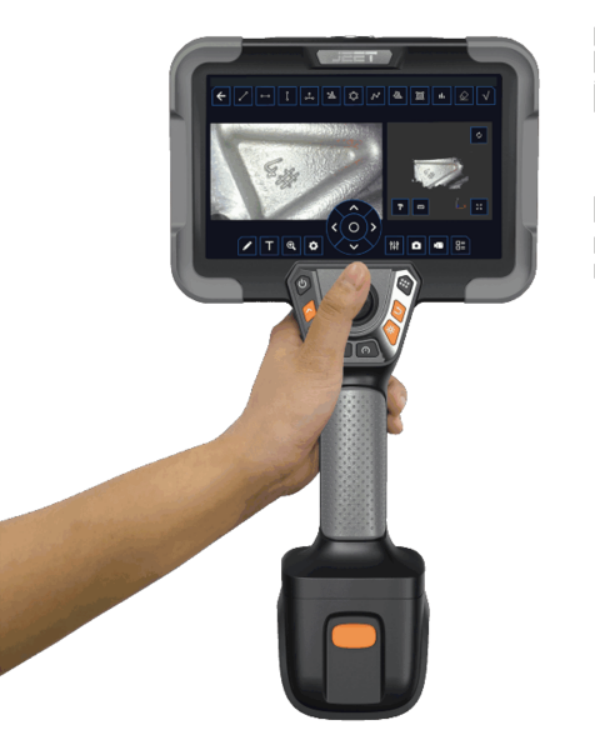